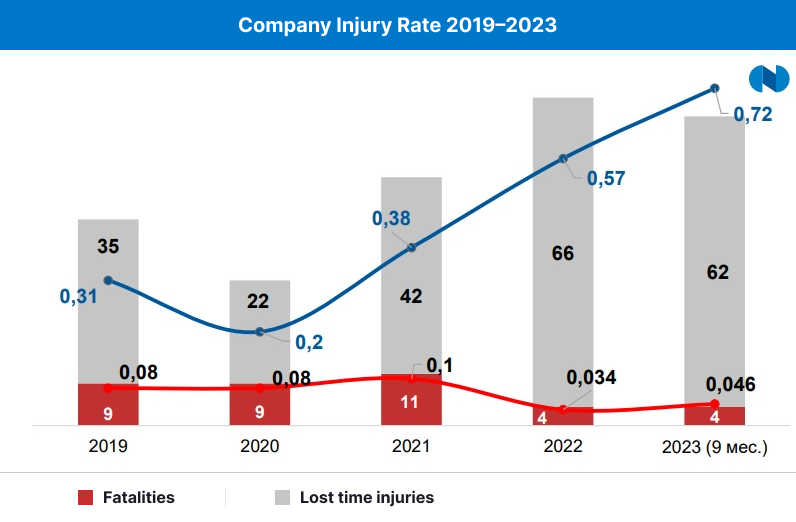
The company’s strategic priority is to achieve zero occupational fatalities. Workplace safety is a cornerstone of Nornickel’s ESG strategy.
To achieve this goal, the company is working to a HSE Strategy which runs until 2025. One of its interim results is a two third reduction in fatal accidents.
Step 1
We revised safety goals and safety performance assessment
In 2021, Nornickel abandoned its focus on numbers and KPIs related to workplace injuries.
These metrics prevented the company from obtaining realistic information on the number of injuries.
In 2022, employee workplace safety was added to management KPIs.
Step 2
We improved the quality of accident investigations
Comprehensive investigations and technical measures that address the root causes of incidents have become a priority. Today, more injuries are identified. This allows for in-depth analysis of various risk scenarios and helps prevent more fatalities. The Incident Investigation Team examines major incidents.
Step 3
We emphasize injury prevention
To achieve zero fatal accidents, management is striving to change workplace safety culture. Updated uniform Essential Workplace Safety Rules have been in effect across Nornickel’s business units since June 2022.
The Essential Rules for Nornickel include six basic rules that cover HSE requirements in all areas (mining, metallurgy, energy, transport) and prohibit:
1) work at height without wearing a safety harness;
2) working in mine operations with a loose and/or untreated roof;
3) loading/unloading operations and cargo movement when there are people in close proximity;
4) undertaking repair and maintenance operations without disconnecting equipment from energy sources, and locking and tagging the energy sources;
5) servicing charged electrical installations and electrical equipment;
6) transporting people and riding in unsuitable vehicles.
To enforce compliance with the Essential Safety Rules, routine preventive audits are carried out to identify and hold accountable persons who fail to comply with the Health, Safety and Environment (HSE) standards.
Step 4
We established an internal HSE coaching system
This is a new addition to Nornickel’s corporate culture. Back in 2014, the company developed a behavioral safety audit program. However, it proved to be ineffective. In 2022, the program was revised, and now the company has 50 coaches.
“In our culture, we habitually focus on weaknesses rather than strengths. Leaders don’t know how to engage with employees. That’s why we organized training to help leaders find an approach to followers and influence their risk orientation. We convey to employees messages which they internalize, and, by doing so, we motivate them to be safe,” says Stanislav Seleznev, Vice President for Environmental Protection and Industrial Safety at Nornickel.
After completing the course, coaches undergo certification and become qualified to train employees. Coaches regularly undergo supervision in order to improve their competencies and maintain training quality.
Today, Nornickel has two coach training programs: a behavioral safety audit (BSA) for leaders and a dynamic risk assessment (DRA) for employees. The first program teaches line managers to communicate with subordinates in such a way as to identify workplace risks in advance, and prevent injuries. The second program teaches employees to identify nearby risks and risks in the workplace, understand their consequences and take appropriate measures.
“We are really proud of our coaching program. There are two things which make training sessions work: good people skills and working through potential scenarios. For example, in everyday life, before sitting down in a chair, we unconsciously check its stability. Many workplace injuries could have been avoided if employees had checked equipment before turning it on,” Stanislav Seleznev points out.
Training sessions take place during work shifts and last eight hours for BSA and four hours for DRA. The training program includes interactive activities and practice — working through specific workplace scenarios. All company employees who have industrial jobs undergo training.
Step 5
We implement cutting-edge safety controls
Across production sites, the company is implementing solutions for real-time PPE detection based on video streaming analysis. These solutions allow managers to not only see if workers are wearing PPE, but also monitor hazardous operations, ensure route compliance, and track the movement of personnel and equipment.
The Nadezhda Smelter has designed a safety management system prototype. Using video streaming analysis, the system detects that an employee entered a high-risk area and directs a beam of light to the floor with a warning message.
The company has been phasing in the automated Control, Management and Safety system. This is a software solution for collecting, recording, and analyzing HSE-related information. The Control, Management and Safety System ensures a uniform approach to monitoring procedures and safety reporting.
Step 6
We create economic incentives for employees
Starting in 2023, employees have been rewarded for identifying workplace risks. To date, the company has identified about 300 risks and paid out more than 2 mln rubles in rewards.
Step 7
We monitor supplier safety performance
Nornickel occupational health and safety (OHS) requirements set the corporate industrial safety standard for contractors. And Nornickel’s internal coaches also train contractors in dynamic risk assessment and behavioral safety audits.
Nornickel is constantly improving its contractor safety management system, and best practice and accumulated experience will drive the process in 2024.
We are now preparing for a significant change in industrial safety and OHS targets for investment project offices, reflecting a shift from reactive to proactive indicators. For example, we will assess how motivated contractors are to create site control systems which identify and eliminate bottlenecks. Project teams addressing safety issues will be assessed.
In February 2024 an information session on how to change project office targeting and debriefing processes saw participants actively involved in discussion about the proposed innovations, in support.
We revised safety goals and safety performance assessment
In 2021, Nornickel abandoned its focus on numbers and KPIs related to workplace injuries.
These metrics prevented the company from obtaining realistic information on the number of injuries.
In 2022, employee workplace safety was added to management KPIs.
Step 2
We improved the quality of accident investigations
Comprehensive investigations and technical measures that address the root causes of incidents have become a priority. Today, more injuries are identified. This allows for in-depth analysis of various risk scenarios and helps prevent more fatalities. The Incident Investigation Team examines major incidents.
Step 3
We emphasize injury prevention
To achieve zero fatal accidents, management is striving to change workplace safety culture. Updated uniform Essential Workplace Safety Rules have been in effect across Nornickel’s business units since June 2022.
The Essential Rules for Nornickel include six basic rules that cover HSE requirements in all areas (mining, metallurgy, energy, transport) and prohibit:
1) work at height without wearing a safety harness;
2) working in mine operations with a loose and/or untreated roof;
3) loading/unloading operations and cargo movement when there are people in close proximity;
4) undertaking repair and maintenance operations without disconnecting equipment from energy sources, and locking and tagging the energy sources;
5) servicing charged electrical installations and electrical equipment;
6) transporting people and riding in unsuitable vehicles.
To enforce compliance with the Essential Safety Rules, routine preventive audits are carried out to identify and hold accountable persons who fail to comply with the Health, Safety and Environment (HSE) standards.
Step 4
We established an internal HSE coaching system
This is a new addition to Nornickel’s corporate culture. Back in 2014, the company developed a behavioral safety audit program. However, it proved to be ineffective. In 2022, the program was revised, and now the company has 50 coaches.
“In our culture, we habitually focus on weaknesses rather than strengths. Leaders don’t know how to engage with employees. That’s why we organized training to help leaders find an approach to followers and influence their risk orientation. We convey to employees messages which they internalize, and, by doing so, we motivate them to be safe,” says Stanislav Seleznev, Vice President for Environmental Protection and Industrial Safety at Nornickel.
After completing the course, coaches undergo certification and become qualified to train employees. Coaches regularly undergo supervision in order to improve their competencies and maintain training quality.
Today, Nornickel has two coach training programs: a behavioral safety audit (BSA) for leaders and a dynamic risk assessment (DRA) for employees. The first program teaches line managers to communicate with subordinates in such a way as to identify workplace risks in advance, and prevent injuries. The second program teaches employees to identify nearby risks and risks in the workplace, understand their consequences and take appropriate measures.
“We are really proud of our coaching program. There are two things which make training sessions work: good people skills and working through potential scenarios. For example, in everyday life, before sitting down in a chair, we unconsciously check its stability. Many workplace injuries could have been avoided if employees had checked equipment before turning it on,” Stanislav Seleznev points out.
Training sessions take place during work shifts and last eight hours for BSA and four hours for DRA. The training program includes interactive activities and practice — working through specific workplace scenarios. All company employees who have industrial jobs undergo training.
Step 5
We implement cutting-edge safety controls
Across production sites, the company is implementing solutions for real-time PPE detection based on video streaming analysis. These solutions allow managers to not only see if workers are wearing PPE, but also monitor hazardous operations, ensure route compliance, and track the movement of personnel and equipment.
The Nadezhda Smelter has designed a safety management system prototype. Using video streaming analysis, the system detects that an employee entered a high-risk area and directs a beam of light to the floor with a warning message.
The company has been phasing in the automated Control, Management and Safety system. This is a software solution for collecting, recording, and analyzing HSE-related information. The Control, Management and Safety System ensures a uniform approach to monitoring procedures and safety reporting.
Step 6
We create economic incentives for employees
Starting in 2023, employees have been rewarded for identifying workplace risks. To date, the company has identified about 300 risks and paid out more than 2 mln rubles in rewards.
Step 7
We monitor supplier safety performance
Nornickel occupational health and safety (OHS) requirements set the corporate industrial safety standard for contractors. And Nornickel’s internal coaches also train contractors in dynamic risk assessment and behavioral safety audits.
Nornickel is constantly improving its contractor safety management system, and best practice and accumulated experience will drive the process in 2024.
We are now preparing for a significant change in industrial safety and OHS targets for investment project offices, reflecting a shift from reactive to proactive indicators. For example, we will assess how motivated contractors are to create site control systems which identify and eliminate bottlenecks. Project teams addressing safety issues will be assessed.
In February 2024 an information session on how to change project office targeting and debriefing processes saw participants actively involved in discussion about the proposed innovations, in support.
August, 2023